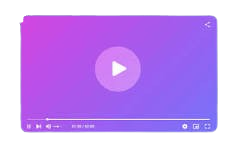
CALF-20, which is an organic metal framework now made industrial to help capture carbon dioxide.Adapted from mfanatomy.com
In May this year, a factory filters worth $ 150 million were opened to capture carbon dioxide in Burnbei, Canada. Redwood, after the longest trees in the world, the facility aims to create enough filters to capture 10 million tons of CO2 Every year, its operator says, Svante TechnologiesWhich indicates the production line as Gigafactory.
The opening of the factory also indicates a commercial penetration of an interesting category of highly invented materials more than 30 years ago that attracted great academic interest and noise-but commercially stumbled. The porous solids that resemble a powder known as organic metal frameworks, or MFS, have dazzled academic chemists for decades.
MFS is organized like molecular scaffolding, which contain wide caves of the interior space – they are the most solid materials in the world. The gram of the MOF powder can have an inner surface area the size of the football field.
Over the past three decades, chemists have invented more than 100,000 MOF species in the laboratory, and tested the ability of powders to store gases, work as an incentive, toxic chemical trap of water and the provision of medicines, among many other possible uses. Scientists have also created relevant materials called coashing organic frameworks, or Cofs. But despite the huge academic interest, chemists were unable to convert materials into industrial products.
Now, SVANTE and other companies hit the idea of using MFS and Cofs to capture carbon. One MOF is now made on the TONNE scale for use in the SVANTE factory. Although it is not clear whether these powders will actually outperform the competing products – the Svante facility also makes other materials to absorb CO2 Shababa Selim, an IDTECHEX analyst, a research consultant in Cambridge, the UK, says the market seems to be opened. Other companies develop MFS to collect water or filter toxic gases. Salim suggests that the MFS market may grow 30 times over the next decade, from $ 30 million to $ 930 million by 2035.
The story of how MFS is on its way into a handful of industrial uses is a typical reality for the development of advanced materials-Decreased academic inventions can take decades to find a commercial purpose. “It seems that carbon capture is a type of application that MFS needs,” says Selim.
Unprecedented properties
The MOF story begins in 1989, when the chemist Richard Robson of the University of Melbourne, Australia, and his colleague Bernard Hoskins announced that they invented a “new and monopolized category of solid polymer materials with unprecedented and possibly useful properties.”1. This was an early description of what might be known as MOF: Repeated structure designed from metal ions linked to long penis -like molecules. Robson mixed copper ions with the organic link particles it made; By choosing the solvent carefully and evaporating slowly, he got these building blocks to crystallize a porous scaffold.
In the mid -1990s, Omar Yaji, a chemist now at the University of California, Berkeley, circulated the term MOF. Some of the initial structures were not stable or only worked at very low temperatures, but Yaghi has developed ways to make MFS more powerful, and build them from the molecular building blocks associated with strong links. Academic laboratories jumped on the idea; More than 100,000 MFS variables are now registered at the Cambridge Crystallographic Data Center, a structural data collection facility. There are more than 100,000 academic papers on the subjects, according to natureAnalysis (see “papers on metal and organic frameworks”).
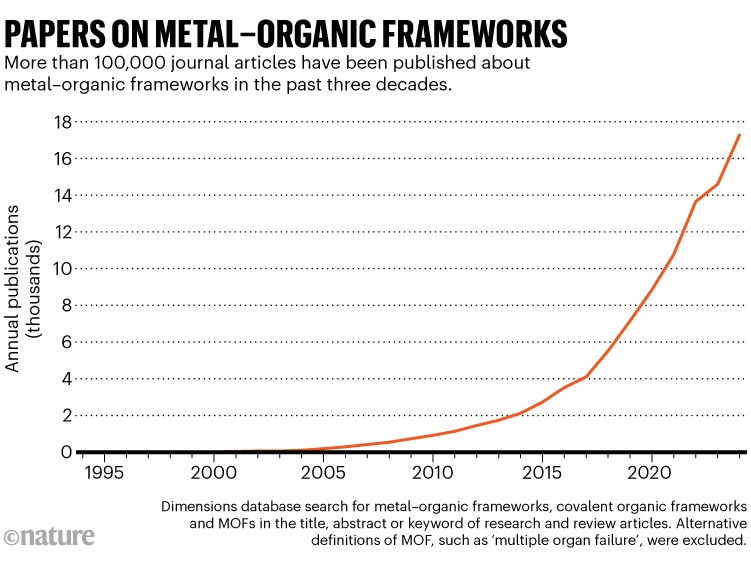
source: nature Analysis/dimensions
Unlike some of the natural materials that are easy to penetrate, such as clay, the inner pores of this artificial size can be carefully and consistent, according to the molecules that make up the scaffolding. Researchers including Yaghi examined how mFs can be dynamic depending on conditions – pressure and temperature can be changed to allow other gases and goods inside and outside the pores.
Chemists also compete to make the material with the largest internal surface space-a title currently carried by MOF called DUT-60, in 2018, with a huge interior surface area of 7,839 square meters per gram2.
All this space has made possible applications wide. For example, chemists have closed the idea that they could store, transport and release hydrogen gas, for example. In the early first decade of the twentieth century, Yaghi, who was then working at the University of Michigan in Ann Arbur, showed that MOF is based in zinc could occupy hydrogen3. This coincided with a step by US President George W. Bush to invest in the “hydrogen economy”, where hydrogen replaces fossil fuels. It was confusing to think about the transportation of hydrogen gas within the MOF Super-Sponges, and its release as required. Global Chemicals Giant Basf was an early investor, and in 2010 she said it was making MOFS on a industrial scale. (The company refused to provide details about this project.)
Today, the talk about the MOF and hydrogen economy is diminished. It is not only the storage of hydrogen as a time-time concept-the displaced on the car engine for electric cars and the Solar Energy Valley cost-but it did not succeed with MFS, partly due to the presence of huge technical challenges about filling a MOF container tank with enough hydrogen efficiently and quickly. Numata In Chicago, Illinois, who conducted doctoral studies at the Yaghi Laboratory. The powders also seemed expensive to provide large standards4. Selim says that existing techniques seem more attractive.
Renewed gravity
But when the correct application comes, researchers can find ways to reduce manufacturing costs. This seems to be a lesson of attention that flourishes the carbon industry in MFS. “Sometimes, for materials, it is about waiting for this market opportunity to pay investment and also made it possible to develop production capacity already, to reduce prices,” Selim says.
Svante’s story explains this. CEO Claude Liturneo says that the company has always focused on removing CO2 An exhaust gases of artificial plants and I did not know how to do so. Svante was trying to develop a “anesthetic” silica for Co2But the materials decompose very quickly to be practical. Letourau contacted the George Academic Group at Calgary University in Canada about the MOF, called CALF-20. These zinc -based physical traps2 The molecules are in their pores, even in the presence of water, which is a major component of the jungle gases. (Many MFS absorb water preferentially – another obstacle to marketing gas storage.)
“I said,“ This is the material we need, ”says Letourau. A year later, he returned, and he has a very simple way to do so.5.
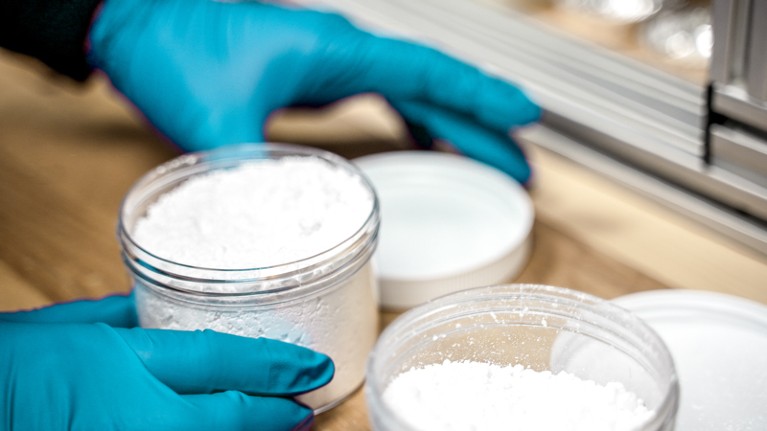
MOF CALF-20, a powder, before using it in Svante’s Carbon Carbing filters.Credit: Svante Inc.
In Svante, the researchers expanded this method to create a kilogram of MOF before cooperating with BASF to develop a multi -length process. BASF now makes Calf-20 Lavanti. Selim says that a number of other companies have turned or renamed to focus on MFS to capture carbon. Promithian particlesIn 2007, the UK University, in 2007, to develop nanoscopic particles, has developed MOF to capture and store carbon, for example.
It is based in Belfast NuadaShe says, she is also developing a MOF store for storage. Nuada is experimenting with carbon capture in a burning facility that produces energy (owned by UNFINIUM) in Knottingley, UK. However, as much as it is publicly known, the BASF -SVANTE process is the only one that is manufactured commercially MOFS commercially, Selim says.
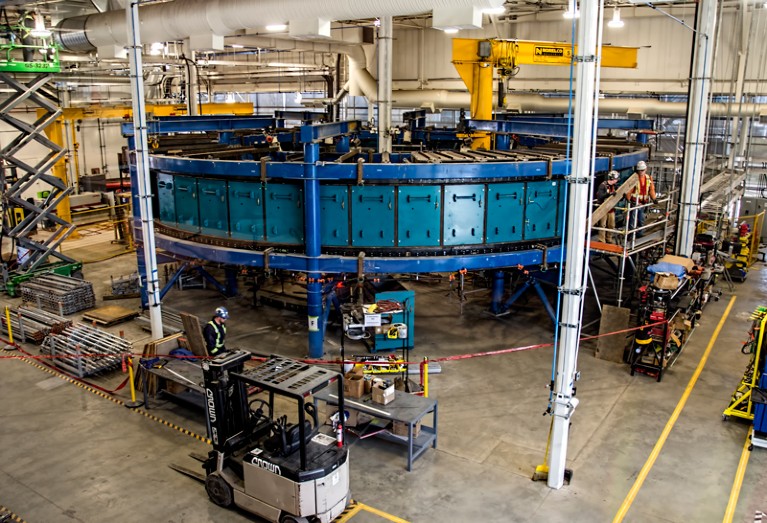
This machine is used in Svante Technologies, organic metal frameworks to capture CO2.Classification: Svante Inc.
Other uses for MFS
MFS may not be suitable for all forms of carbon capture. It absorbs a company2 Directly of air is more difficult than absorbing from exhaust gases from artificial plants, due to the CO decrease2 concentration. Although SVANTE supplies carbon sticks to a direct air escalating company called Climeworks in Zurich, Switzerland, it is not based on MFS, says Letourau says, but on the chemicals usually used to capture carbon, which is called walled amateurs.
However, in October 2024, Yaghi stated that its research team was able to make COF that pulled CO2 Directly from the air – promising development. He says that his team simplifies the synthesis of that article and expands its scope6.
The Yaghi team also presses the MFS to harvest water from the air. It has shown a MOF-based device in Death Valley, California, built of a material called MOF-303 that can absorb water vapor at low humidity7. This MFS trick is that only a change in a small temperature is needed to release the besieged water, allowing it to be collected with a decrease in temperature overnight in the desert. Yaghi founded company called ATOCLE In Irvin, California, “Test of Water Rosary Units before Trade” using MOF, says. Startup Airjoule In Ronan, Montana, it also aims to capture direct water; In June this year, a deal with an unveiled developer signed his database to integrate his MOF water harvest into those facilities.
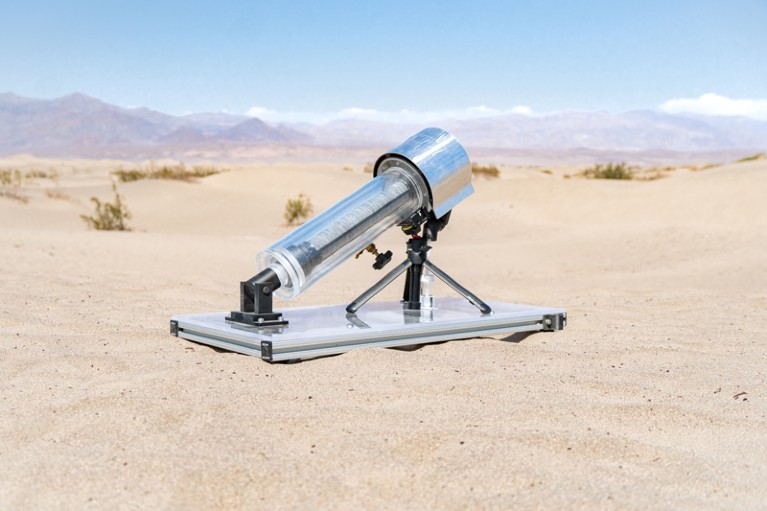
A trial for the harvesting of MOF water in the Valley of Death, California. Credit: Yaji Laboratory, University. California